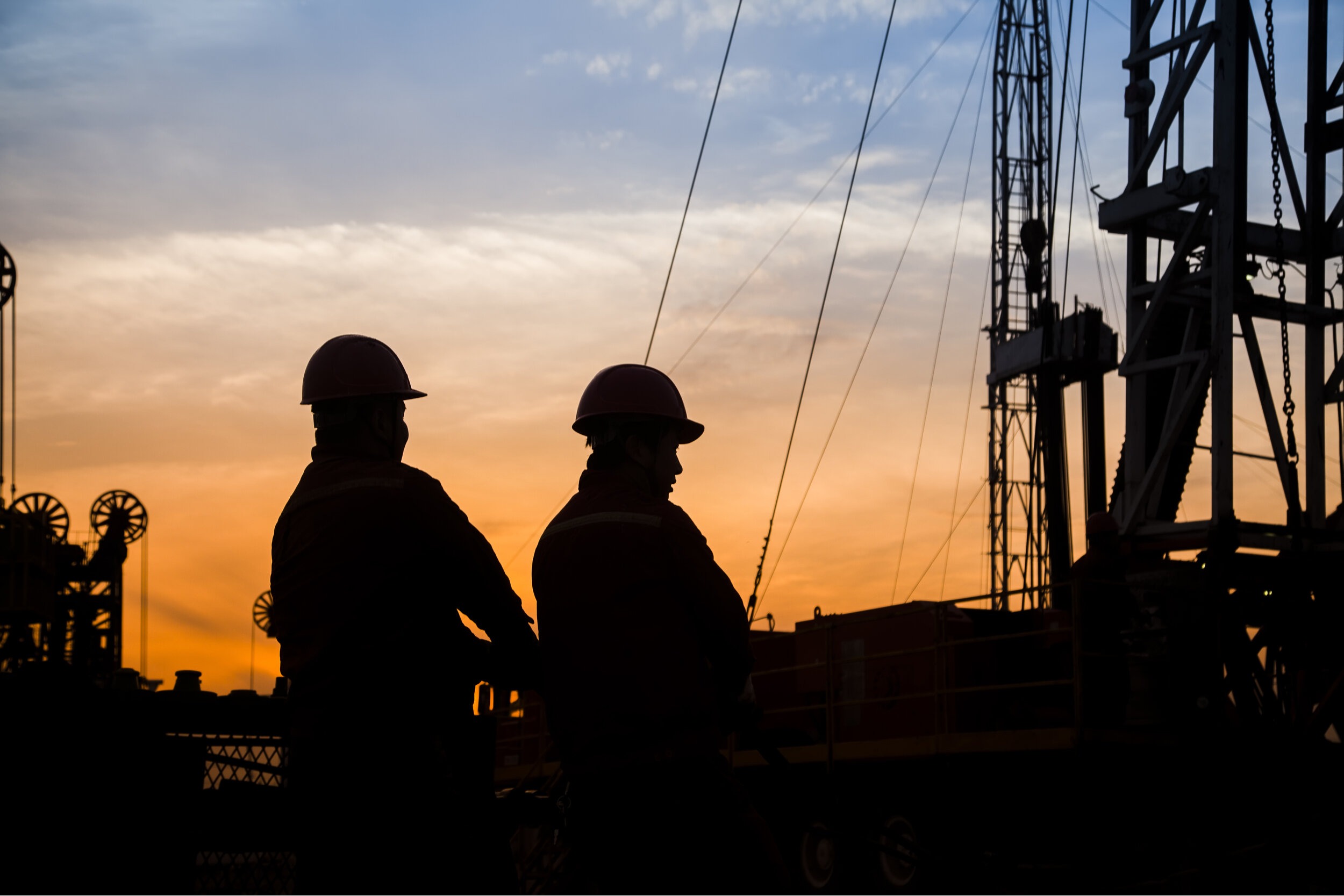
The role of the drilling mud engineer is one of the most important on the rig. Traditionally the mud engineer or drilling fluids engineer is responsible for testing the mud during drilling operations and recommending additives to maintain mud weight, mud properties and chemistry with the goal being to keep the mud within the designed specifications according to the drilling plan.
Why is this important? Maintaining wellbore pressure during drilling is critical. If the mud density is too low, formation pressure can cause the borehole to collapse; conversely if the mud density is too high, an overbalance state will occur, causing lost circulation and formation damage. In worst case scenarios, a formation ‘kick’ can cause a well blowout.
Daily mud tests and reporting
The drilling fluids/mud engineer manages the mud program to parameters set by the operators drilling plan. This is done by performing a series of daily mud checks and tests. Every day and sometimes multiple times a day the mud engineer will perform a mud check or test to determine the mud properties at different points in the drilling program.
The report is filled out by the mud engineer and the data he enters is used to calculate hydraulics on the rig for that day. Newer programs include functions for hydraulics modeling. This can be done daily or whenever the drilling company requests the information.
What happens if a problem is encountered? For a formation problem that is affecting the mud in a negative way the drilling fluids engineer determines the point of contamination and then adjusts the fluid properties to treat the mud accordingly. Drilling fluids are inhibitive. You do not want to hydrate the formation, especially when drilling through shale, which has a strong affinity for water. You may encounter carbonates, saltwater flows or gas; these all can affect the mud in different ways.
While there have been advances in mud reporting, hydraulics modeling and digital archiving of the daily mud test, the day-to-day activities of the wellsite mud engineer and the mud mixing system have changed very little.
Benefits of a combined fluids and solids control program
A more recent concept is that of the total fluids management approach. This combines the many fluids-related systems under a single competition fluids design management program and can include the initial drilling fluids system selection, wellsite equipment for solids removal, closed-loop systems and haul-off and disposal. This puts the traditional ‘mud’ engineer at the center of the fluids management program.
One example is the collaboration of the drilling fluids engineer and solids control expert. Working together they operate solids control equipment and maintain the solids concentration, keeping it to a low level. The goal is to reduce solids content in the mud, resulting in reduced disposal volume and fluid waste services requirements. This combination can streamline the process to make the total system as efficient as possible for the operator while reducing costs.
- Make recommendations on the drilling mud circulation (closed-loop) system to reduce the amount of solids content in the mud and keep overall solids control down
- Reduce disposal, both amount of solids, liquids and transportation costs
- Streamline activities for more efficient operations
- Reduce overall fluids systems cost to operator
Expertise needed for a successful well
Operators using this new combined management approach enjoy added benefits. However, the drilling fluids management company must have the actual experience and expertise to make it work. This includes the knowledge to select the best fluid system for the formation and the rig and then integrate the additional oilfield services equipment to the existing rig system. It includes expertise to evaluate new and existing technology, additives and systems to ensure a good fit for the well. During drilling, this expertise is used to make adjustments so the system performs at the highest levels. Finally, the drilling fluids engineer must have the experience to anticipate what to expect from the formation, foresee what problems may be encountered, and take steps to prevent them from happening. For example, pretreating the mud based on knowledge of the formation or weighting the mud for an upcoming interval.
The Panther Advantage
The fluids experts at Panther Fluids Management understand the interaction between the different fluid systems at the wellsite. Our system designs are backed by years of experience and have consistently lowered overall fluid and well costs for our customers.
Not only do we consult with the operator to design the best fluids system for each well; we understand the importance of collaboration throughout the project, from closed-loop systems for solids control to oilfield trucking, including haul-off and disposal. And most important, we understand the total fluids life cycle and can prepare for many contingencies based on well conditions. Contact Panther Fluids Management today for the latest in drilling fluids treatment systems and technology.
- Consistent approach and proven process for efficient fluid systems design
- Independent lab testing for unbiased testing results and no overhead for physical lab costs
- Experience in different geographies, well types and drilling environments including offshore, HPHT, deep wells, horizontals, critical wells and environmentally sensitive areas.
- Combined 140+ years overall expertise in fluids management
- 100% incident free haul off and disposal
Panther Fluid Management has the experience to assist your company with all of its solids and fluid disposal needs. Our system designs are backed by years of experience and have consistently lowered overall mud costs for clients. We consult with the operator to design the best fluids system for each well; including everything from discrete services like mud and shakers screens to fluids engineering to complex closed-loop systems for solids control to haul-off and disposal. More importantly, we understand the total fluids life cycle and can prepare for many contingencies based on well conditions. Contact Panther Fluids Management today for the latest in drilling fluids technology.